Process Engineering
OPTIMISATION AND MONITORING OF PRODUCTS RELATED PROCESS
Our team of skilled technicians supports companies in solving problems and achieving the highest standards of quality and performance through material testing, optimization of the production process and equipment. Consulting and fine-tuning activities are carried out at our customers’ production sites or directly at our molding island. Proplast has the latest generation of presses and automatisms and a new compounding line equipped with the thermoplastic foam extrusion station for the production of lightened products and reduced use of chemical additives. Recently installed is the 3D printer with which innovative material formulations for Additive Manufacturing are tested.Our team of skilled technicians supports companies in solving problems and achieving the highest standards of quality and performance through material testing, optimization of the production process and equipment. Consulting and fine-tuning activities are carried out at our customers’ production sites or directly at our molding island. Proplast has the latest generation of presses and automatisms and a new compounding line equipped with the thermoplastic foam extrusion station for the production of lightened products and reduced use of chemical additives. Recently installed is the 3D printer with which innovative material formulations for Additive Manufacturing are tested.
-
Compounding
-
Extrusion
-
Injection molding
-
Compression molding
-
Thermoforming
-
3D Printing
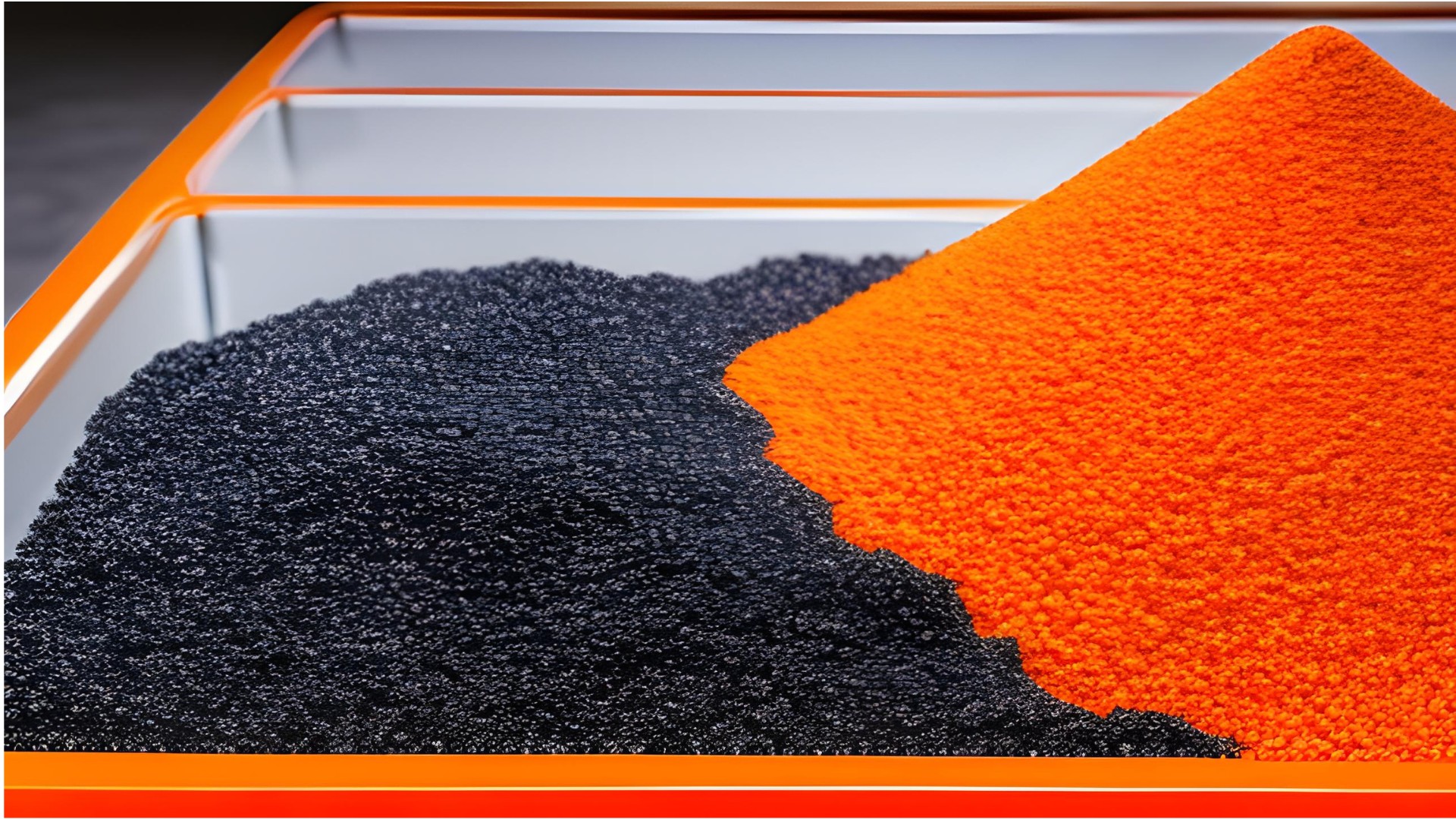
Compounding
With the equipment of our technical area, we are able to produce formulations of thermoplastic polymers, both commercial and experimental, with additives and fillers with different shape, size and chemical nature. We can work with granules, flakes, powders and liquids. Moreover, we produce polymeric blends, working with different polymers, from simple polyolefins to polyamides, polyurethanes, bio-based and biodegradable polymers, up to recycled materials. We manufacture small compound batches and samplings (up to 500 kg) through lab and pilot-scale twin screw co-rotating extruders, also pre-mixing granules and fillers by dry-blend, when necessary. Proplast is the right partner both to optimize new formulations to be placed on the market and to produce small batches of compounds.
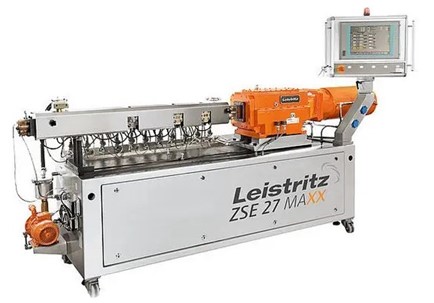
Sheet extrusion
Our consolidated experience in several types of polymeric materials allows us to perform sheet extrusion fine-tuning, producing samples with a nominal width of 200 mm and a thickness ranging from 200 micron and 1 mm. In collaboration with our R&D team, the optimization of processing parameters and their correction, if necessary, is performed with a careful monitoring based on customer’s requirements in order to maximize the quality of the product. A further strength of Proplast facilities is represented by the physical expansion of thermoplastic materials by supercritical CO2 through Promix technology. This process allows obtaining parts with a markedly reduced weight but with performances like unexpanded parts. Finally, Proplast is at disposal with its competences in testing materials like PVC using specific tools and technologies.
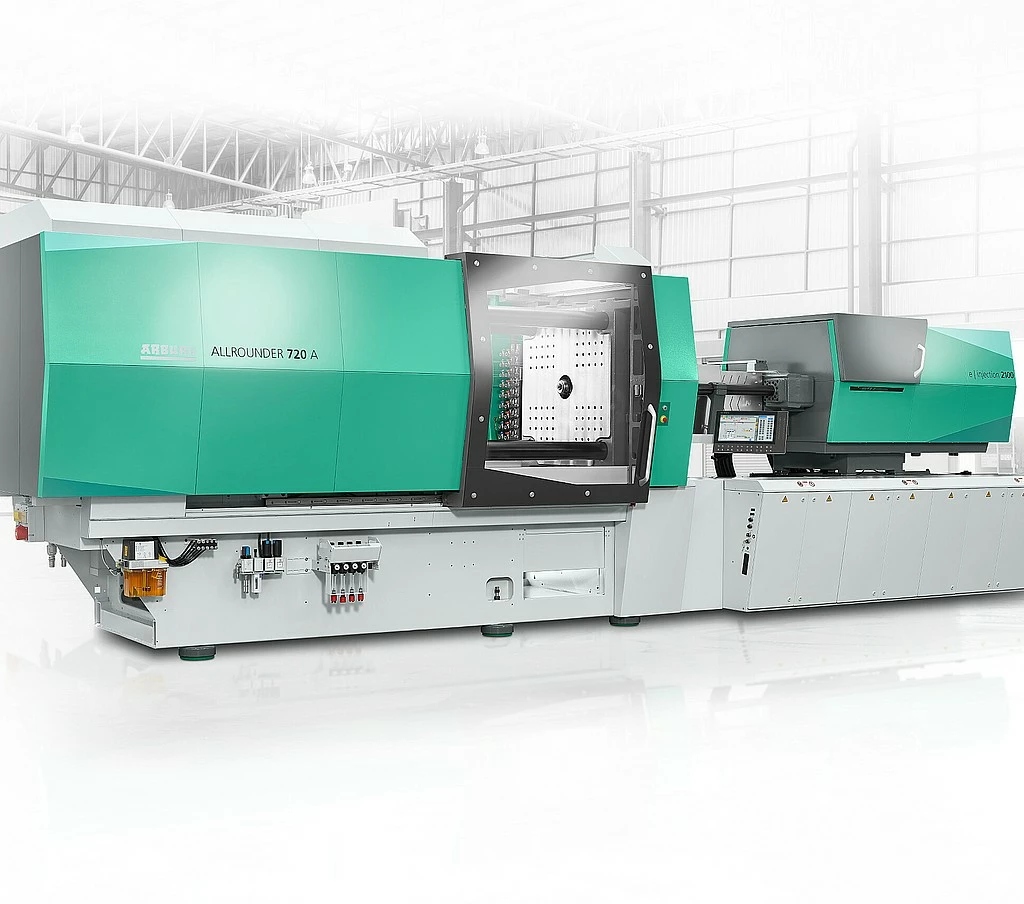
Injection moulding
We have been supporting and optimizing processes parameters since ever, throughout mold testing and evaluation, and preparation of small sample batches to validate the development phase before passing to a production phase. Our technicians perform precise monitoring of injection molding parameters, together with dimensional and functional checks. Effective solutions for each kind of productive need are achieved combining the use of innovative technologies and the analysis of testing data. Several innovative manufacturing techniques are together gathered in Proplast’s facilities. This aspect represents a paramount opportunity for our customers due to the fact we can easily support them in enhancing physical, mechanical, and aesthetical properties of their products and, therefore, incrementing their productivity. Finally, we are able to produce pre-series samplings, offering to our customers a productive advantage if they need to test new products before commercializing them and building final moulds. Proplast, with its long experience and consolidated flexibility, is actually a reliable partner on the market to produce small batches (from 500 to 5000 pieces), using not only pilot mould built in our internal workshop but also with mould of the customers.

Compression molding
With our new vertical compression moulding machine (clamping force 40 tons), we can perform R&D activities on both materials and technology, exploiting the cooling and heating system of the mould during the process. Moreover, this kind of machine is equipped with a specific plastification system which can be used for compression moulding of rubbers.
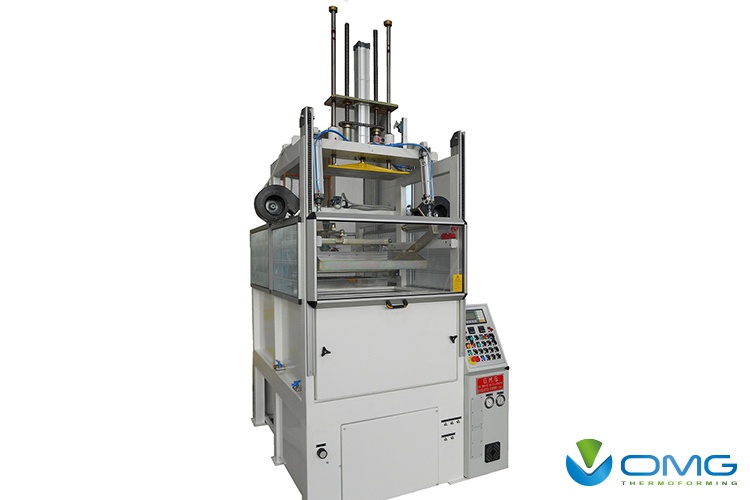
Termoforming
With our pilot-scale thermoforming machine, we can produce small batches of thermoformed pieces, also using biocomposites. Thanks to the experience of our technicians, we are able to optimize processing parameters adapting them to different types of polymeric materials. Thermoformed components are compliant to customers’ features and requirements and their compliance can be evaluated with a complete chemical, physical and rheological characterization in our laboratories.
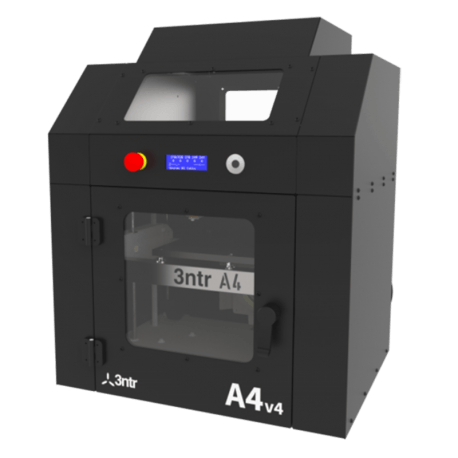
Stampa 3D
With the help of open source machines present at Proplast, we are able to combine the freedom of geometry (inherent in 3D printing) with the freedom of materials and their characteristics. High expertise in formulation development on polymeric materials is also applied to FDM technology to further expand the potential of 3D printing technology. We can therefore produce material samples and/or directly spools of wire for FDM with the characteristics required by the customer.
New technologies for innovative products
Consulting and specialized services for injection and compression molding, extrusion, cast filming, compounding, thermoforming, thermoset composite infusion, 3D printing
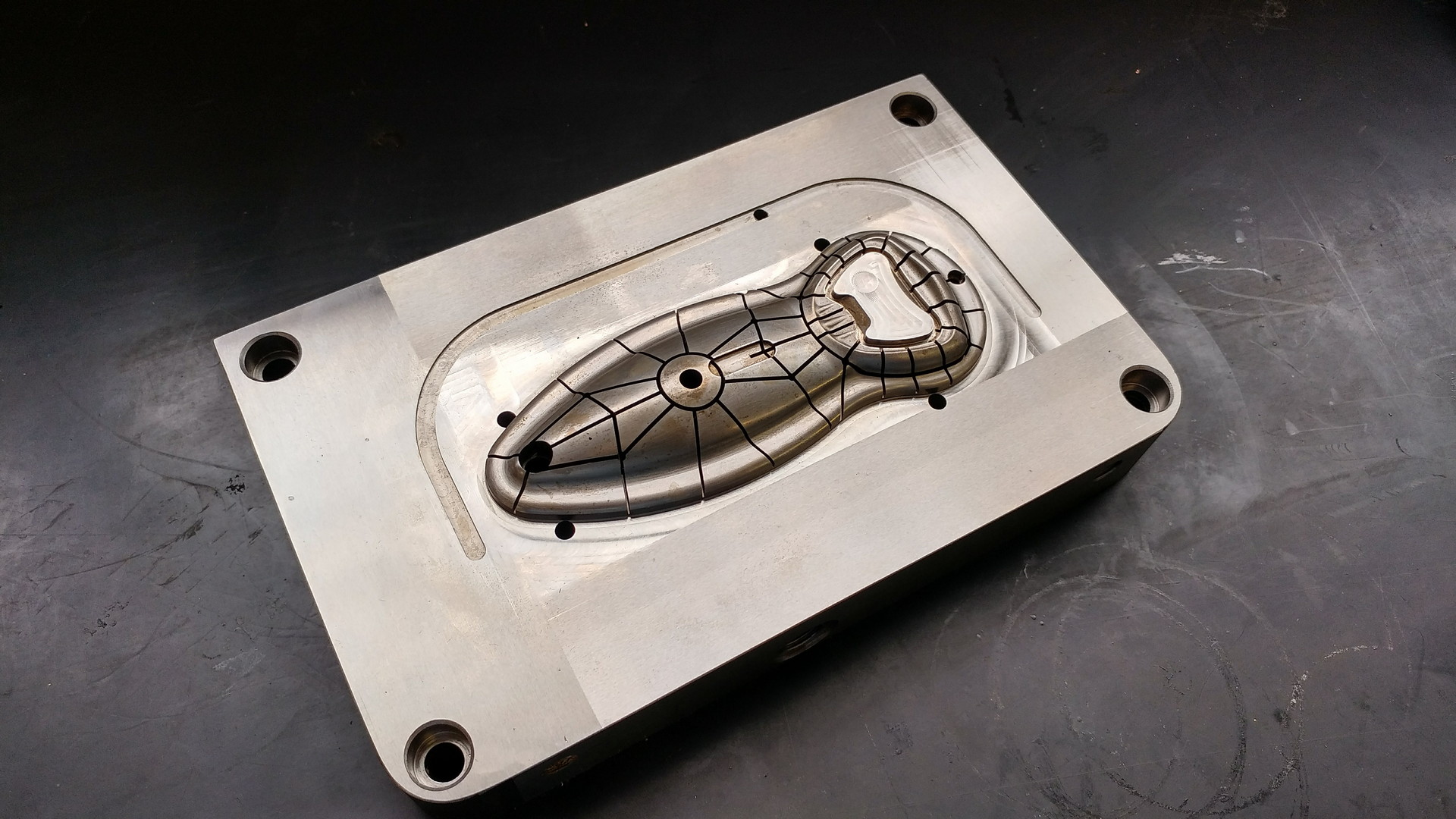
The Bottle Opener project
Hybrid molding
Lightness, performance and mass production compatible volumes are the advantages of thermoplastic composite laminates. Here's how to design, process, and simulate their characteristics and performance.
- Metal replacement
- excellent weight-performance ratio
- high efficiency
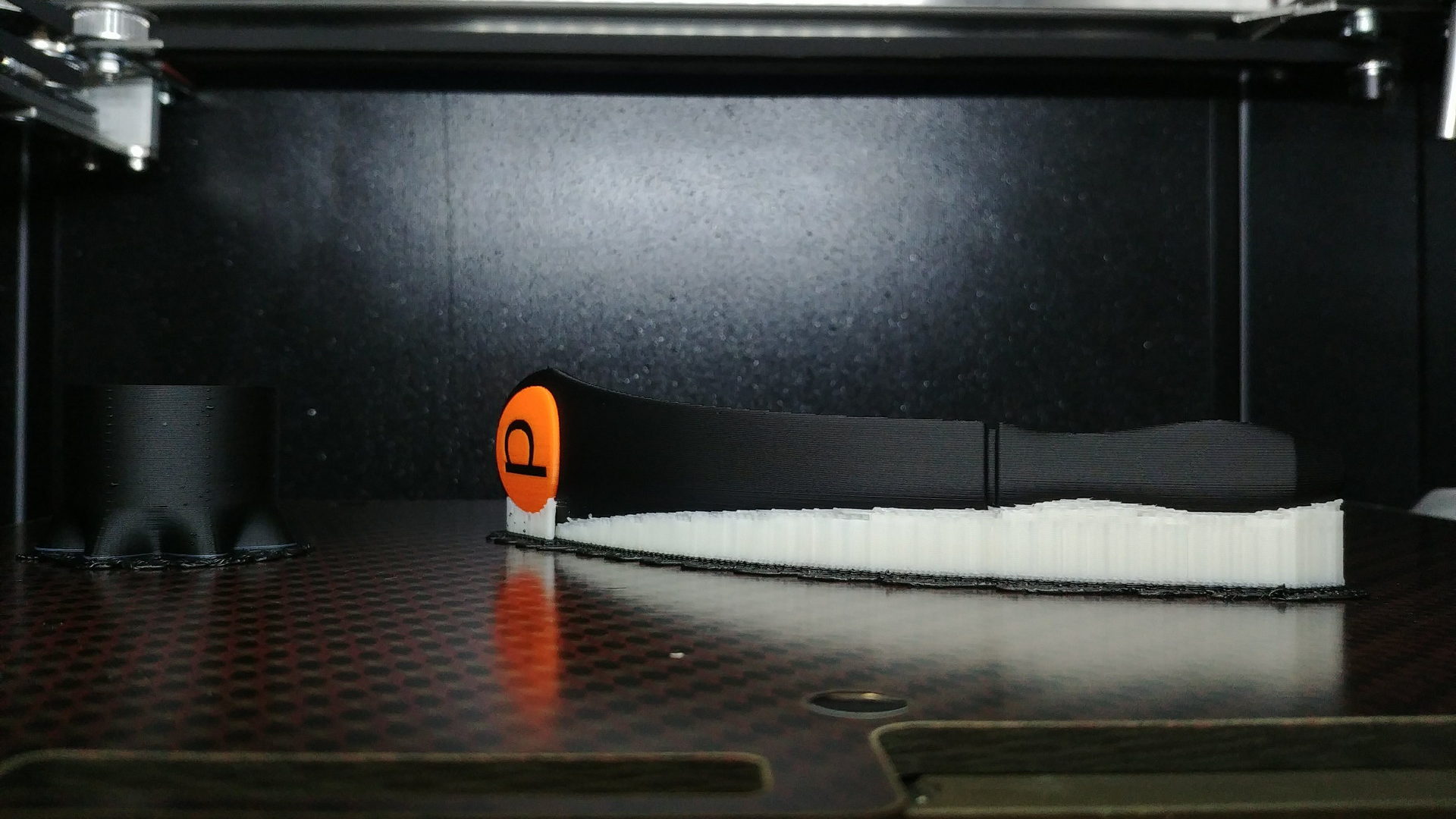
Stylus Pen 3D
Ad hoc materials formulation for Additive Manufacturing.
A video to introduce our customers and members to the expertise of Proplast researchers in the field of selecting and formulating improved materials for a wide variety of Additive Manufacturing applications. Attraverso questo video abbiamo voluto valorizzare le attività di ricerca, di compounding, di estrusione dei materiali e dei filamenti, di testing, di design, di engineering e di Additive Manufacturing.
- Additive Manufacturing
- selection and formulation of improved materials
Some equipment in the department:
EQUIPMENT | MANUFACTURER | MODEL |
Injection molding machine 7 Ton | Babyplast | 610P |
Injection molding machine 50 Ton | Arburg | 370 S 500 – 170 |
Injection molding machine 120 Ton | Engel | Victory 120 EcoDrive |
Injection molding machine 250 Ton | Arburg | 630 A 2500 1300 |
Anthropomorphic robot | Kuka | Agilus KR 10 R1100 SIXX |
Cartesian robot | SEPRO ROBOTIQUE | 8U20 |
2K molds | PLASDAN | EL.0300 |
MICROGEL | FRIGEL | |
DUE SISTEMI DI DEUMIDIFICAZIONE | MORETTO | |
COROTATING TWIN SCREW EXTRUDER | LEISTRITZ | ZSE 27 MAXX-40D |
COUNTER-ROTATING TWIN-SCREW EXTRUDER | BAUSANO | MD 19/30 |
SINGLE SCREW EXTRUDER FOR CAST FILM | BG PLAST | SD 30/30 |
MINI SPINNING EXTRUDER FOR 3D PRINTING | 3DEVO | |
MONOEXTRUSION | TECOM OFFICINE MECCANICHE SRL | POLIFILM 25 F.S/TAV.350 |
VERTICAL INJECTION AND COMPRESSION MOLDING MACHINE FOR RUBBER | COMI | C40 |
FORCED VOLUMETRIC DISPENSER | PRT | |
BLADE MILL WITH DUST COLLECTOR | CMG | G25-30 |
SORTING LINE (PROTOTYPE) | NOVASIS | P00-2020 |
BENCHTOP THERMOFORMING MACHINE | OMG | MA 18 |
Industrial 3D printer | 3NTR | A4 |