Innovative Technologies
CONTINOUS INTERACTION WITH COMPANIES TO BE AT THE FOREFRONT
Proplast offers a wide range of consulting services, solutions and applied technologies for the design, simulation and prototyping activities of polymeric artifacts. Our team, composed of specialized technicians, is able to follow all the phases preceding mass production: from the avamproject to product engineering aided by advanced multiphysics simulations, up to the realization of pilot molds for small samples. We also play an active role in rapid prototyping taking advantage of the benefits of additive technology. Constant interaction with companies enables us to offer the best customized solutions in terms of performance, time and cost optimization.
-
ALL
-
Cost reduction
-
Aesthetic improvement
-
Performance enhancement
-
Monitoring and optimization
-
Rapid Prototyping
-
MuCell® Microcellular physical expansion
-
Heat & Cool - Dynamic mold conditioning
-
RocTool® - Mold induction conditioning
-
CO2 Spot Cooling - Ultra-fast mold cooling
-
Kistler - Monitoring of pressures in cavities
-
Composite Hybrid Molding - Backinjection of thermoplastic composite laminates
-
Promix Solutions - Microcellular physical expansion in extrusion
-
Flex Flow - Obturation system for independent control of the obturators
-
3D Printing - Component and material development for additive manufacturing
MuCell® - Microcellular physical expansion
Technology concerning the physical expansion of polymer by mixing it with nitrogen in a supercritical state. The MuCell® process, dedicated to technical products, decreases the viscosity of thermoplastic resins by injecting small amounts of gas into the melt and creates a microcellular structure in the product through the expansion of gas into cavities. Injecting the polymer with nitrogen in the supercritical state, inside the mold, provides several benefits such as:
- weight reduction of molded parts
- Elimination of suctions in the whole detail
- maximum reduction of internal stresses
- cycle time reduction
- Lowering the viscosity of the polymer
- Reducing the clamping force required by the injection machine
Cavity molds
- expansion compensates post-pressure
- lower closing force
- lower design constraints
- cycle time reduction
Injection unit
- lower viscosity
- best filling
- Ad hoc gate design and placement if possible
- decrease in temperature and thus energy
Finished piece
- peso minore
- strong reduction of deformations
- fewer withdrawals
- strong reduction of suctions
Equipment used: Trexel S11-TE-10
Download the sample preliminary study and related R.O.I. with MuCell technology. Contact us for preliminary study on your product. Available Engel Victory 120 tons injection molding machine for real MuCell trials.
Heat & Cool - Dynamic Mold Conditioning
Technology to enhance the aesthetic quality of plastic products achieved through dynamic mold conditioning. The Heat & Cool® process consists of dynamic temperature variation of the cavity surface at each molding cycle to achieve a molded part with high surface quality. The polymer perfectly reproduces the mold surface, whatever it is: glossy, satin, with different textures, logos, holograms etc. The use of this technology also makes it possible to remove the seam lines that occur whenever two streams of polymer meet during soldering. The benefits that can be achieved are:
- high aesthetic degree
- faithful reproduction of textures on the figure
- Elimination of joint lines in the molded part
- Possibility of decreased injection pressures as the progressive cooling of the material is less pronounced
Aesthetic improvements
- excellent surface quality, glossy or matte
- invisible seam lines
- brilliance of blacks and colors
- absence of halos
- Reduction of defects due to gate marks, streaks
Technical improvements
- possible reductions in thickness
- better propagation of holding pressure
- suction reduction
- decrease in temperature and thus energy
Equipment used: Vario Therm REGLOPLAS Vario G3/4 200°C
RocTool® - Mold Induction Conditioning
Technology that promotes rapid heating of molds through electromagnetic induction. Plastic material is injected into the mold cavity at high temperature. RocTool® technology also allows the optimal cooling curve to be designed, ensuring the best material properties and molding cycle. Roctool induction heating technology is the most advanced heating and cooling process. Fast. Reliable. Economical. The ability to rapidly heat the mold and fully control temperature distribution opens up new molding possibilities, including reducing cycle times, increasing part quality, and extending flow length. An immediate return on investment.
- viscosity reduction in injection phase
- increased flow length
- thin thickness filling
- injection pressure reduction
- increase mechanical properties of joints
Aesthetic improvements
- glossy surface qualities (gloss, Piano Black...)
- possibility of eliminating painting
- texture quality and embossed surfaces (matte, gloss reduction....)
- seam lines not visible
Technical improvements
- compaction improvement
- suction reduction
- dimensional stability
- warpage reduction
- elimination injection marks, streaks....increased crystallinity and mechanical properties
- Better propagation of holding pressure
- Material entry into a very hot cavity
CO2 Spot Cooling
Technology that allows very rapid cooling of localized pointacs of the mold and difficult to reach with traditional water conditioning. By taking advantage of the expansion of CO2 in specially targeted spot areas of the mold, a large amount of heat is removed in a very short time. The rapid cooling of hard-to-reach areas of the mold dramatically reduces cycle times.CO2 Spot Cooling also enables the elimination of hot spots and the conditioning of very thin and deep taps, thus achieving more effective and faster cooling than conventional systems.
Benefits
- Significant reduction in cooling time and, consequently, cycle time
- hot spots elimination
- uniform mold temperature
- Very thin male conditioning
- liquid coolants and hydraulic seals are not required
Equipment used: LINDE CO2 Mold Spot Cooling
Kistler - Monitoring of pressures in cavities
Technology that allows continuous monitoring, through the use of in-cavity sensors, of the pressures developing inside the molded figures. The detected pressures make it possible to keep the monitored figures perfectly under control at the points of interest and to analyze in real time all the molds as well as the production trend in order to obtain molding cycles free of reject parts. Cycle analyses also allow,to keep under control the trend of pressures to which many variations of variable unknowns can be traced both at the level of cavities, temperatures, viscosity and indirectly of the auxiliary systems on board the machine.
Vantaggi
- production process control
- quality control
- possibility during startup and first mold trials to find the ideal molding condition not only from machine parameters but also from mold parameters
Equipment used: KISTLER Type 5887 A
Composite Hybrid Molding - Backinjection of thermoplastic composite laminates
Technology that enables the manufacture of thermoplastic composite components of high mechanical performance by combining continuous fiber structural reinforcement with highly geometrically complex parts made by injection molding. The process of hybrid molding of composites possesses the great advantage of allowing these components to be obtained in a single production step, in which the laminate - once heated by infrared lamps - is inserted into the injection mold and thermoformed from the mold closure, while at the mold closure the back-injection process takes place.
Benefits
- high mechanical performance
- technology particularly suitable for metal replacement
- easy industrial scalability
- Reduced cycle times, typical of injection molding
- Reduced use of chemical reagents compared with thermoset composites
- greater eco-sustainability
- Exceeding the shelf life limit of thermoset systems
Equipment used: Proplast – Forno compositi termoplastici Unico FCT18PLT | Automazione isola di lavoro KUKA-ENGEL / SEPRO-ARBURG
Promix Solutions - Microcellular physical expansion in extrusion
Promix Solutions technology is one of the most important innovations and breakthroughs in compounding and extrusion. The process involves the creation of lightened products characterized by a cell structure. A fluid under supercritical conditions, carbon dioxide or nitrogen, is injected into the polymer melt in a manifold (foam system) located between the plasticizing screw and the extrusion head. Mixing is ensured by the joint action of a series of static mixers to dissolve the supercritical component within the molten polymer, resulting in a single phase. The principle of profile expansion is due to the pressure drop at the extrusion head. The drop in pressure generates an abrupt phase separation: the fluid previously dispersed in the melt loses the supercritical conditions by moving to a gaseous state and simultaneously with the cooling of the polymer causing the formation of gas cells (nucleation phase) and their progressive accretion (growth phase). The technology is flexible and adaptable to different polymers and application fields such as extrusion of pipes and profiles, foils and sheets for thermoforming.
Benefits
- homogeneity of melt temperature
- Greater control over cell distribution
- non-flammable
- applicable to all polymers
- ecofriendly: physical expansion without the use of expanders
Equipment used: Promix – EXPANSION SYSTEM WITH SUPERCRITICAL CO2
Flex Flow - Obturation system for independent control of the obturators
FLEXflow technology is the ultimate solution for precise control of pressure and material flow during the injection molding process. The servo-controlled plugging system independently monitors each plug allowing the operator to adjust the filling pressure to reduce pressure drop and the appearance of flow marks on the part.
Benefits
- Surface quality improvement, for large "class A" surfaces, embossed, aesthetic components, etc.
- high process repeatability
- safe, clean and dry (no oil, no liquids)
- ease of maintenance and use
- optimal flow balance
- Reduction of deformation on the part
- Reduction in press tonnage (up to 20%)
3D printing - Component and material development for additive manufacturing
3D printing is the most advanced manufacturing technology for making components by depositing successive layers of material. Proplast provides equipment and expertise in the development of specific materials for FDM technology through the possibility of developing specific formulations, making filaments and validating them on 3D printing machines.
Benefits
- high customization of components
- low cost of tooling
- possibility of using a wide range of materials
-
MuCell® Microcellular physical expansion
-
CO2 Spot Cooling - Ultra-fast mold cooling
-
Promix Solutions - Microcellular physical expansion in extrusion
MuCell® - Microcellular physical expansion
Technology concerning the physical expansion of polymer by mixing it with nitrogen in a supercritical state. The MuCell® process, dedicated to technical products, decreases the viscosity of thermoplastic resins by injecting small amounts of gas into the melt and creates a microcellular structure in the product through the expansion of gas into cavities. Injecting the polymer with nitrogen in the supercritical state, inside the mold, provides several benefits such as:
- weight reduction of molded parts
- Elimination of suctions in the whole detail
- maximum reduction of internal stresses
- cycle time reduction
- Lowering the viscosity of the polymer
- Reducing the clamping force required by the injection machine
Cavity molds
- expansion compensates post-pressure
- lower closing force
- lower design constraints
- cycle time reduction
Injection unit
- lower viscosity
- best filling
- Ad hoc gate design and placement if possible
- decrease in temperature and thus energy
Finished piece
- peso minore
- strong reduction of deformations
- fewer withdrawals
- strong reduction of suctions
Equipment used: Trexel S11-TE-10
Download the sample preliminary study and related R.O.I. with MuCell technology. Contact us for preliminary study on your product. Available Engel Victory 120 tons injection molding machine for real MuCell trials.
CO2 Spot Cooling
Technology that allows very rapid cooling of localized pointacs of the mold and difficult to reach with traditional water conditioning. By taking advantage of the expansion of CO2 in specially targeted spot areas of the mold, a large amount of heat is removed in a very short time. The rapid cooling of hard-to-reach areas of the mold dramatically reduces cycle times.CO2 Spot Cooling also enables the elimination of hot spots and the conditioning of very thin and deep taps, thus achieving more effective and faster cooling than conventional systems.
Benefits
- Significant reduction in cooling time and, consequently, cycle time
- hot spots elimination
- uniform mold temperature
- Very thin male conditioning
- liquid coolants and hydraulic seals are not required
Equipment used: LINDE CO2 Mold Spot Cooling
Promix Solutions - Microcellular physical expansion in extrusion
Promix Solutions technology is one of the most important innovations and breakthroughs in compounding and extrusion. The process involves the creation of lightened products characterized by a cell structure. A fluid under supercritical conditions, carbon dioxide or nitrogen, is injected into the polymer melt in a manifold (foam system) located between the plasticizing screw and the extrusion head. Mixing is ensured by the joint action of a series of static mixers to dissolve the supercritical component within the molten polymer, resulting in a single phase. The principle of profile expansion is due to the pressure drop at the extrusion head. The drop in pressure generates an abrupt phase separation: the fluid previously dispersed in the melt loses the supercritical conditions by moving to a gaseous state and simultaneously with the cooling of the polymer causing the formation of gas cells (nucleation phase) and their progressive accretion (growth phase). The technology is flexible and adaptable to different polymers and application fields such as extrusion of pipes and profiles, foils and sheets for thermoforming.
Benefits
- homogeneity of melt temperature
- Greater control over cell distribution
- non-flammable
- applicable to all polymers
- ecofriendly: physical expansion without the use of expanders
Equipment used: Promix – EXPANSION SYSTEM WITH SUPERCRITICAL CO2
-
Heat & Cool - Dynamic mold conditioning
-
RocTool® - Mold induction conditioning
-
Flex Flow - Obturation system for independent control of the obturators
Heat & Cool - Dynamic Mold Conditioning
Technology to enhance the aesthetic quality of plastic products achieved through dynamic mold conditioning. The Heat & Cool® process consists of dynamic temperature variation of the cavity surface at each molding cycle to achieve a molded part with high surface quality. The polymer perfectly reproduces the mold surface, whatever it is: glossy, satin, with different textures, logos, holograms etc. The use of this technology also makes it possible to remove the seam lines that occur whenever two streams of polymer meet during soldering. The benefits that can be achieved are:
- high aesthetic degree
- faithful reproduction of textures on the figure
- Elimination of joint lines in the molded part
- Possibility of decreased injection pressures as the progressive cooling of the material is less pronounced
Aesthetic improvements
- excellent surface quality, glossy or matte
- invisible seam lines
- brilliance of blacks and colors
- absence of halos
- Reduction of defects due to gate marks, streaks
Technical improvements
- possible reductions in thickness
- better propagation of holding pressure
- suction reduction
- decrease in temperature and thus energy
Equipment used: Vario Therm REGLOPLAS Vario G3/4 200°C
RocTool® - Mold Induction Conditioning
Technology that promotes rapid heating of molds through electromagnetic induction. Plastic material is injected into the mold cavity at high temperature. RocTool® technology also allows the optimal cooling curve to be designed, ensuring the best material properties and molding cycle. Roctool induction heating technology is the most advanced heating and cooling process. Fast. Reliable. Economical. The ability to rapidly heat the mold and fully control temperature distribution opens up new molding possibilities, including reducing cycle times, increasing part quality, and extending flow length. An immediate return on investment.
- viscosity reduction in injection phase
- increased flow length
- thin thickness filling
- injection pressure reduction
- increase mechanical properties of joints
Aesthetic improvements
- glossy surface qualities (gloss, Piano Black...)
- possibility of eliminating painting
- texture quality and embossed surfaces (matte, gloss reduction....)
- seam lines not visible
Technical improvements
- compaction improvement
- suction reduction
- dimensional stability
- warpage reduction
- elimination injection marks, streaks....increased crystallinity and mechanical properties
- Better propagation of holding pressure
- Material entry into a very hot cavity
Flex Flow - Obturation system for independent control of the obturators
FLEXflow technology is the ultimate solution for precise control of pressure and material flow during the injection molding process. The servo-controlled plugging system independently monitors each plug allowing the operator to adjust the filling pressure to reduce pressure drop and the appearance of flow marks on the part.
Benefits
- Surface quality improvement, for large "class A" surfaces, embossed, aesthetic components, etc.
- high process repeatability
- safe, clean and dry (no oil, no liquids)
- ease of maintenance and use
- optimal flow balance
- Reduction of deformation on the part
- Reduction in press tonnage (up to 20%)
-
Composite Hybrid Molding - Retroiniezione di laminati compositi termoplastici
-
Flex Flow - Sistema di otturazione per il controllo indipendente degli otturatori
Composite Hybrid Molding - Backinjection of thermoplastic composite laminates
Technology that enables the manufacture of thermoplastic composite components of high mechanical performance by combining continuous fiber structural reinforcement with highly geometrically complex parts made by injection molding. The process of hybrid molding of composites possesses the great advantage of allowing these components to be obtained in a single production step, in which the laminate - once heated by infrared lamps - is inserted into the injection mold and thermoformed from the mold closure, while at the mold closure the back-injection process takes place.
Benefits
- high mechanical performance
- technology particularly suitable for metal replacement
- easy industrial scalability
- Reduced cycle times, typical of injection molding
- Reduced use of chemical reagents compared with thermoset composites
- greater eco-sustainability
- Exceeding the shelf life limit of thermoset systems
Equipment used: Proplast – Forno compositi termoplastici Unico FCT18PLT | Automazione isola di lavoro KUKA-ENGEL / SEPRO-ARBURG
Flex Flow - Obturation system for independent control of the obturators
FLEXflow technology is the ultimate solution for precise control of pressure and material flow during the injection molding process. The servo-controlled plugging system independently monitors each plug allowing the operator to adjust the filling pressure to reduce pressure drop and the appearance of flow marks on the part.
Benefits
- Surface quality improvement, for large "class A" surfaces, embossed, aesthetic components, etc.
- high process repeatability
- safe, clean and dry (no oil, no liquids)
- ease of maintenance and use
- optimal flow balance
- Reduction of deformation on the part
- Reduction in press tonnage (up to 20%)
-
Kistler - Monitoring of pressures in cavities
Kistler - Monitoring of pressures in cavities
Technology that allows continuous monitoring, through the use of in-cavity sensors, of the pressures developing inside the molded figures. The detected pressures make it possible to keep the monitored figures perfectly under control at the points of interest and to analyze in real time all the molds as well as the production trend in order to obtain molding cycles free of reject parts. Cycle analyses also allow,to keep under control the trend of pressures to which many variations of variable unknowns can be traced both at the level of cavities, temperatures, viscosity and indirectly of the auxiliary systems on board the machine.
Vantaggi
- production process control
- quality control
- possibility during startup and first mold trials to find the ideal molding condition not only from machine parameters but also from mold parameters
Equipment used: KISTLER Type 5887 A
-
3D Printing - Component and material development for additive manufacturing
3D printing - Component and material development for additive manufacturing
3D printing is the most advanced manufacturing technology for making components by depositing successive layers of material. Proplast provides equipment and expertise in the development of specific materials for FDM technology through the possibility of developing specific formulations, making filaments and validating them on 3D printing machines.
Benefits
- high customization of components
- low cost of tooling
- possibility of using a wide range of materials
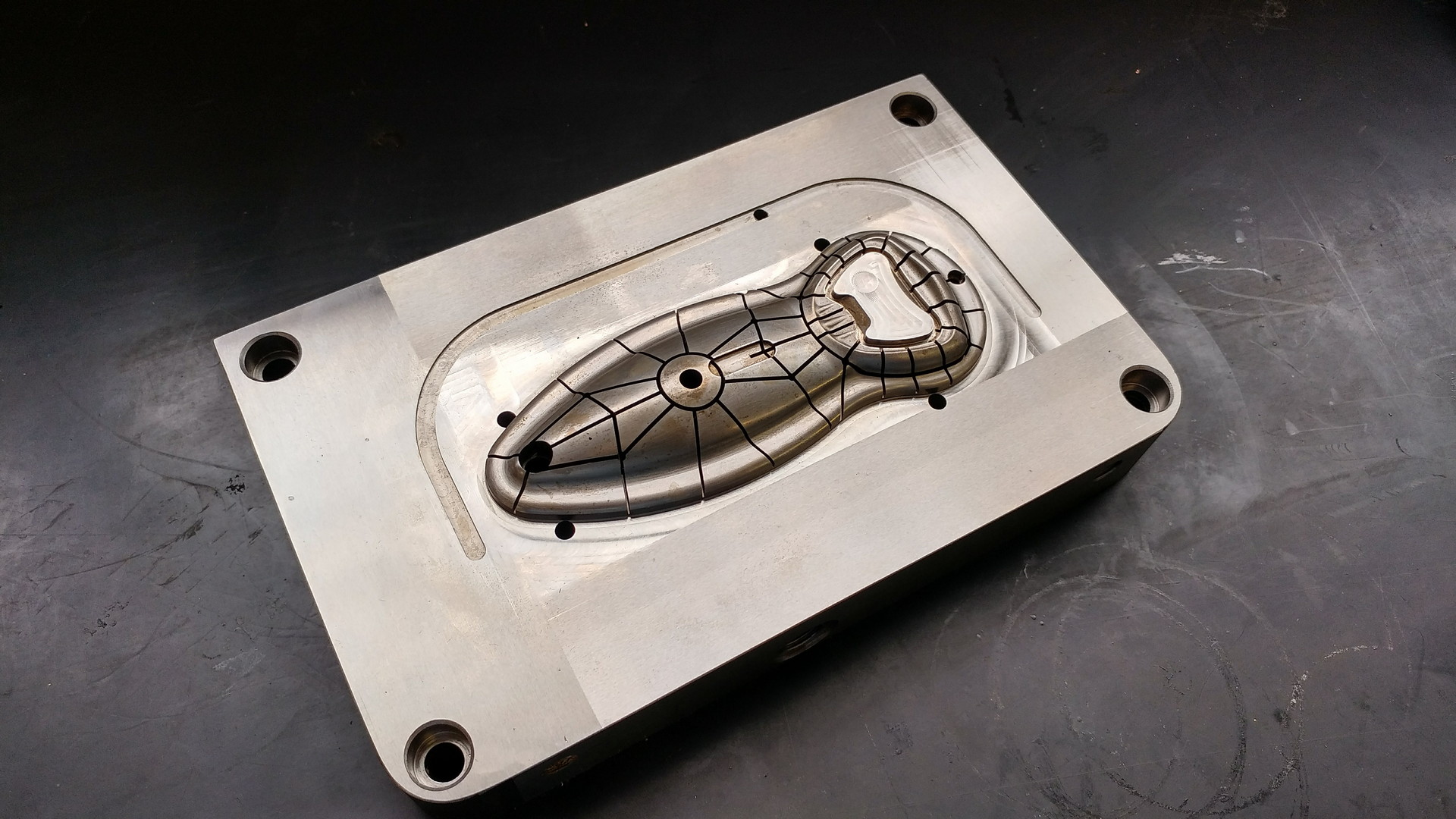
The Bottle Opener project
Hybrid molding
Lightness, performance and mass production compatible volumes are the advantages of thermoplastic composite laminates. Here's how to design, process, and simulate their characteristics and performance.
- Metal replacement
- excellent weight-performance ratio
- high efficiency
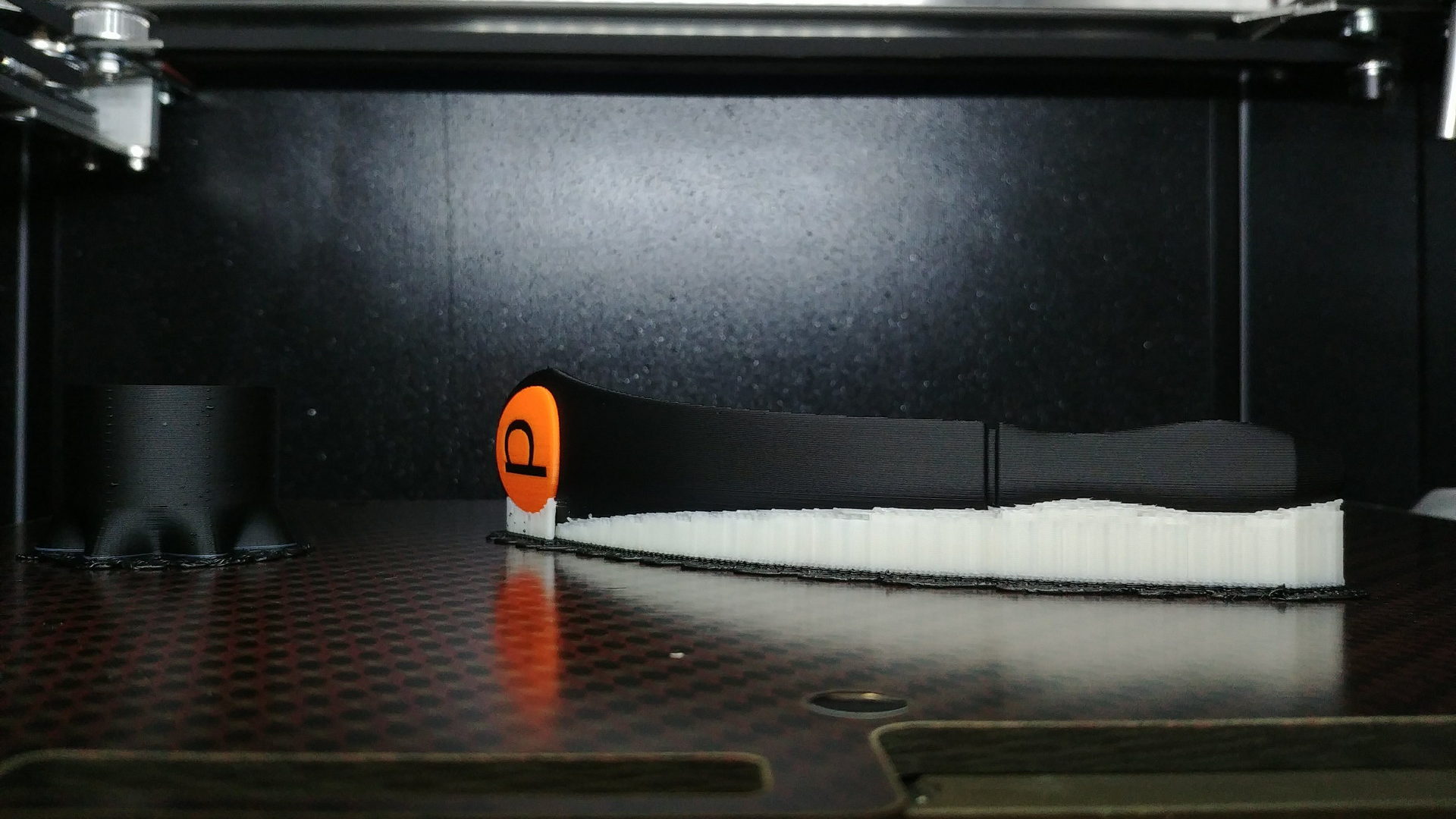
Stylus Pen 3D
Ad hoc materials formulation for Additive Manufacturing.
A video to introduce our customers and members to the expertise of Proplast researchers in the field of selecting and formulating improved materials for a wide variety of Additive Manufacturing applications. Attraverso questo video abbiamo voluto valorizzare le attivitĂ di ricerca, di compounding, di estrusione dei materiali e dei filamenti, di testing, di design, di engineering e di Additive Manufacturing.
- Additive Manufacturing
- selection and formulation of improved materials